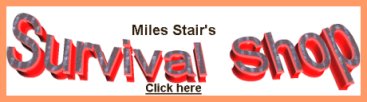
MAKING CANDLES
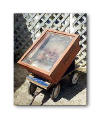
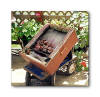
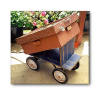
MAKE YOUR
OWN CANDLE WICKS
Wicks can be made from any pure
cotton string or twine. Thick string will provide
more light, and is more suitable for larger diameter
candles. Use a thin string for taper or votive
candles. But cotton string "sputters" when burned
unless it is first treated with boric acid. Take a
roll or ball of cotton string and find a container
into which it will fit completely, but not with a lot
of excess room. Then make a solution of one (1)
tablespoon of salt and two (2) tablespoons of Borax
per cup of boiling water -- that IS the boric acid solution.
Weigh down the ball of string in the container so it
won't float up (find a rock), and pour in the boric
acid solution, making sure you have enough to
completely cover the cotton string. Let is soak for
several days, then let it dry in the sun for several
more days. If there are excess salt crystals covering
the string, just wash them off with water and dry the
ball of string again. Now you have the wicking
necessary for making a lot of candles, cheap and
easy!
HOME MADE
CANDLE MOLDS
A candle mold can be any smooth
sided, tapered metal container. For example, I use
empty 14 ounce salmon cans for molds, as they have
smooth sides and the slight taper necessary for the
candle to be easily removed. Punch a small hole with
an ice pick through the center of the bottom of the
mold. Push the wick through the hole from the bottom,
then pull it up enough so you can tie it to the
center of a 16 penny nail. The nail will hold the top
of the wick in the center of the mold. Turn the mold
upside down and pull the wick tight, and seal the
hole with a pinch of plumber's putty. Now the
wick can be cut off about an inch from the putty, and
the mold is ready to accept the melted wax or
paraffin. Make at least a half dozen such molds with
the wick centered and tight at one time. The
plumber's putty can be reused many times before it
gets hard and no longer seals, so it is very
inexpensive in use.
MAKING CANDLES
|
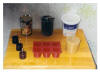 |
The first step is to place the
molds into a shallow pan of water, such as the bottom
pan from a broiler "borrowed" from the kitchen. Put
about a half inch of water into the pan, then put the
molds into the water filled pan. The reason for the
water is that you ARE going to spill some wax, and
when the wax hits the water it will solidify and be
easy to remove and melt again. But if the melted wax
falls onto a dry surface, it sticks!
The next step in candle making is
to pour the melted paraffin at a temperature of at
least 180 F into the molds: any cooler than that and
the candles have a wrinkled surface. You will find
that as the paraffin or wax cools it shrinks
considerably. Once cool, the final step is to pour in
enough paraffin to fill the depression in the candle
caused by the shrinkage.
To remove the candle from the
mold, the wax must be cold. First remove the
bit of plumber's putty from the bottom of the mold,
then tug on the nail and the candle should come out.
If it doesn't come out easily, then cut off the wick
just below the nail and pound the mold gently on an
old board. If the candle doesn't release from the
mold then, it means the wax is still too warm and has
not shrunk completely. The cooling process then can
be speeded up by placing the candle molds into a pail
of cold water, or into a freezer for a half
hour. "Candle wax" (paraffin) has a "phase
transformation" at about 50 degrees F, where it
shrinks about 5%, so actual freezing is not
necessary. Wait a few minutes after removing
the mold from the freezer to allow the mold itself to
warm up, and the candle should come out of the mold
easily. If it does not, then warm water poured
over the mold will expand the mold and then the
candle should come out.
Taper and votive candles are more
difficult to remove from the molds. Candles that
cannot be removed from molds, due to a rough interior
surface of the mold, etc, can be removed by pouring a
little boiling water over the mold, but that is
rarely needed. Then pour boiling water into the mold
to remove any roughness caused by old wax, and scour
well, and the mold is restored to duty.
Remember to make candles outside,
as spilling wax is virtually guaranteed! But since
paraffin and wax easily melt at about 150 F, and a
tea kettle can heat water to over 212 F, clean up
simply means boiling water. Hot, liquid wax dropped
on a kitchen carpet, however, is extremely difficult
to remove, so guys, melt it outside on the patio and
keep peace in the house.
MAKING CANDLES
USING A KEROSENE STOVE TO MELT THE
WAX |
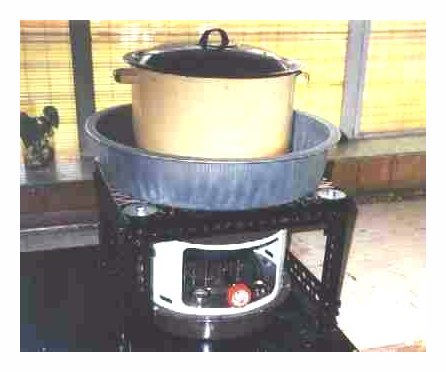 |
In the winter, candles may be made
using a kerosene stove on a patio table to melt the
wax, but with cautions: paraffin is very
flammable, and it melts at only 150 F, so place a
wide, thin pan* on the stove, fill it with water at
least 2" deep, then melt the wax in an old stock pot.
The water surrounding the stock pot will act as a
heat buffer, transferring enough heat to the stock
pot to easily melt the wax, and any drips will fall
safely into the water.
* This pan can be a metal pet food
tray, a metal oil drain pan, a "hog tray," or any pan
at least 12" wide and 3 or 4 inches high.
USING A SOLAR
OVEN TO MELT WAX IN THE SUMMER |
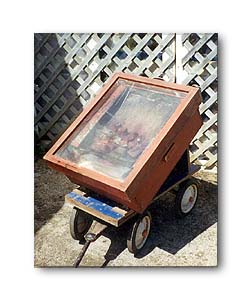 |
On a normal summer day without
clouds, my solar melter will melt about 4 bread pans
of paraffin per day, which is sufficient for about 20
large salmon can candles that will burn for about 24
hours each. Because the solar melter will produce 200
degree melted paraffin in less than two hours of
direct sunlight, large scale production of candles
means having a lot of molds, as the wax does not cool
fast enough to recycle molds within 2 hours. I
normally work with at least 20 molds, for
example.
When working with a solar oven
and 200 degree paraffin, remember that everything is
HOT, so you will need to wear a pair of leather
gloves. As the gloves will get wax on them, it is
better to have a pair of gloves set aside for just
that purpose.
Here is my routine when using the
solar oven for melting wax. At about 10:00 AM, I tow
the solar oven from under cover and point it East, so
the shadow from the sun falls about 6 inches to the
left side of the raised solar oven. The cover to the
unit is removed, and bread pan full of recycled
candle wax is placed on the melting tray. There is
already another bread pan under the drain end of the
tray covered with a piece of aluminum window screen,
which acts as a filter.
Before noon, the sun's shadow is
about 6 inches to the right side of the solar melter,
and the wax is melted and holding about 200 degrees
F. Another bread pan full of recycled wax chunks is
ready. The lid of the oven is quickly removed and the
melting tray removed and laid flat on the ground. The
bread pan of wax chunks is scattered in the hot
melting tray. Next, the window screen filter is
removed from the pan of melted paraffin in the solar
melter and placed on the spare, now empty bread pan.
Very carefully - and wearing leather gloves -
the bread pan of hot liquid paraffin is removed from
the oven and placed flat on the ground. The empty
bread pan is placed in the oven, then the melting
tray, the lid/cover of the solar oven is replaced,
and finally the oven thermometer is placed back
through the hole in the upper part of the solar oven.
This process takes less than 2 minutes, as I want to
retain as much heat as possible in the solar
oven.
The hot bread pan full of melted
wax is very carefully carried to the candle molds and
the wax poured into the previously prepared molds
while still as hot as possible. The quality of the
candle is directly related to the temperature at
which the paraffin is when poured into the mold.
Wax at 155 degrees makes very ugly, wrinkled
candles, as the wax cools too fast on contact with
the metal sides of the mold. Wax poured at about 200
degrees heats up the mold sufficiently to produce
smooth sided candles that are pretty.
The next step is to return to the
solar melter and turn it to again be slightly past
the sun, so as the sun moves across the horizon the
angle of the sun's heat rays is directly into the
solar oven, then moves slightly past.
The final steps are to fill the
now-empty bread pan with more chunks of paraffin,
used candle wax, reclaimed drippings from a
commercial candle maker, whatever you can find
inexpensively, and get more molds set up with wicks
strung between a nail and plumber's putty, as in two
hours or less they are going to be needed again!
MAKING
CANDLES PRETTY
As candles come from the mold,
they are not generally pretty - there can be
wrinkles, surface imperfections, etc. When
candles are mass produced with a large quantity of
melted wax from a stock pot or solar melter, however,
is not the time to worry about that. Once you
have a large supply of candles, then you can make
them pretty. Candles may be held by the wick
with a pair of pliers and dipped in hot water, and
the surface melts just enough to give candles a hand
made appearance. Candles may also be dipped in a
different color melted wax or dipped into wax in
which little speckles have been added, giving them a
very unique look.
For information on making
traditional candles, candle molds, etc, please visit
ArtNCandle.
------------------
Site
Index
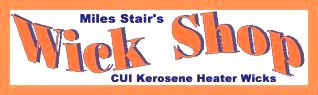