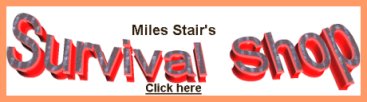
PLAYING
WITH TEMPERATURES
Temperature - heat and cold - changes
the actual physical properties of things, and is easy to
use to help us make or repair things, or even make our
own tools.
A
very useful
railroad spike!
Making steel tools for various specific purposes
has long been done by the person who wants and needs the
tool. Again, using temperatures properly can make a hard
job much easier. Leaf spring or file steel has incredible
quality, and can be worked rather easily if first
softened by a process called annealing. Place the
steel to be annealed into a fireplace or wood stove, heat
it to a cherry red, then let it cool naturally, and it
will be annealed.
The annealed steel can then be cut, drilled, and
shaped as desired. While still soft it is then sanded and
filed to very near the final finish, including buffing if
desired, then heated again to a cherry red and then
immediately quenched completely in oil, a process called
tempering. The oil-bath tempering restores a spring-steel
quality of temper. Then the oil scale is removed, final
buffing done, the finish edge applied (as in a knife),
and the tool is ready for use. Cold water quenching makes
steel harder, but brittle.
The size of the tool desired is used as a gauge
for what size steel to use to make it. Wood rasps make
fine knives or scrapers, needing only to be swaged into
shape when annealed. Swaging is cold-forming of steel
with a hammer and anvil. The combination of annealing,
swaging, and tempering can be used to fix bent leaf
springs used in many applications.
Let us assume you have a collapsed "V" shaped spring in
one of your tools. First the spring is annealed, then it
is gently swaged to its original shape, then tempered,
and it is almost as good as new. Pioneer gunsmiths
restored leaf springs over campfires in the
wilderness.

Heating steel makes it expand
slightly, while rapid cooling makes it shrink, or
contract, slightly. Using those principles the pioneers
could put a steel rim onto a wooden wagon tire in the
middle of nowhere. The rim was formed to be slightly
smaller in diameter than the wheel, then heated in a
campfire to a red color, quickly placed around the wooden
rim, then shrunk to a tight fit by splashing the hot
steel with cold water. The steel would be brittle from
the cold water quench, so better wagon smiths quenched
with oil of some kind, even lard or fat.
That same principle can be used to attach bands of steel
around shafts, for example to attach a pulley or a sleeve
to strengthen a bent rod or shaft. The sleeve or pulley
is boiled while the shaft is frozen, thus expanding the
sleeve and contracting the shaft. If the sleeve was
drilled slightly smaller than the shaft, it will now fit
over it, and as the temperatures equalize the band or
sleeve becomes tightly bound to the shaft.
Primitive welding can be done with the process of
hot swaging. Say you want to make a steel band to
reinforce a tank. The band is first annealed, then swaged
round to the final diameter when cold. Then the
overlapping ends of the band are heated cherry red and
hammered together on an anvil while hot. The process may
have to be. repeated several times, but the ends of the
band will become "welded" together and stay firmly
attached. A gasoline or propane torch can be used for
"spot" heating for this purpose, thus confining the heat
to a specific spot. If a fire is used instead, tongs or
vice grips must be used to hold the steel while swaging,
as the heat cannot be localized as with a torch.
 |
 |
The knife and
sheath above illustrate that an outstanding and very
useful knife can be made with materials at hand.
A large file was annealed twice, hand forged to shape,
ground, sharpened, then hardened in a two-step
process, the back of the blade being spring temper and
the edge only being knife hard. The knife can
thus be used as a machete, clearing brush and chopping
down small trees, or be a fine combat knife if called
upon to do so. The sheath was made from plastic
cut from a thick blue 50 gallon barrel, glued and
riveted together. If the blade is kept clean and
oiled so that it does not rust, the knife and sheath
should last for the remainder of my lifetime and
another as well. |
Three knives
hand forged from old files. The handles were made
from dry hardwood found in the forest, shaped and riveted
in place using nails for rivets and copper pennies as
washers. |
The leather
for the sheath was from an old tractor implement power
belt found in an abandoned barn, hand riveted so the
knives all nest as shown above. The cost? Some
nails, rivets, and pennies. |
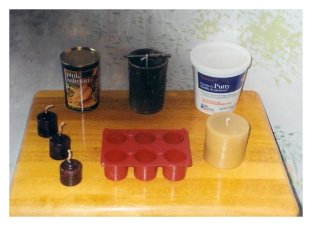
Working with wax making candles or as
a beekeeper? A tea kettle can be your best friend. Take
wax, for example. It melts at 145 F, so boiling water
(212 F) can melt it easily. A brief dip in hot
water loosens a candle from a mold, and soaking in
boiling water will clean the mold. Have a candle gang
mold and the candles are stuck? Freeze the mold,
and the wax and mold will contract. Thawing expands
the mold faster than the wax, and the candles should come
out easily. If not, a little boiling water from a
whistling tea kettle over the mold will expand the mold
and the candles will come out easily. Then pour boiling
water into the mold to dissolve whatever was causing the
candles to stick. See more in Making
Candles.
Boiling water poured through a honey
filter turned inside-out will melt the wax particles and
residue right off.
Propolis is remarkably sticky and tenacious at room
temperature. But freeze it and propolis becomes brittle
and can be "popped off" frames. Heat an old but sturdy
frame in a solar melter and the wax will melt off,
leaving the propolis which will be soft and easily
scraped away.
Encounter cartridge brass that is too
hard (old) and getting split necks, and you need that
brass for reloading? Anneal the neck and shoulder
area and the brass will become soft and last another 20
rounds or so before annealing is again needed. The
details of annealing cartridge brass can be found in
Reloading
.410 shotshell cases.
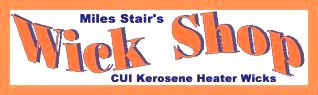
Site
Index